废钢预热连续水平加料电炉基本工艺操作规程(实际冶炼操作)
2022/5/10 16:44:13 来自:
河南泰航节能科技发展有限公司 浏览次数:0
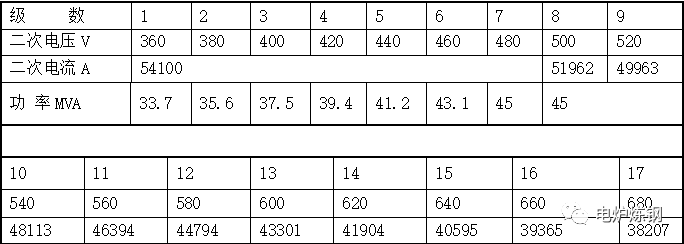
装第一批料,以8~10级电压手动供电,熔清后停15~20分钟后加入第二批料,再以8~10级电压手动供电,熔清后停15~20分钟左右后加入第三批料,以8~10级电压手动供电;基本熔清停30分钟左右后启动康斯迪加料,以10~13级电压手动供电。如因料罐小,进料次数多,熔清后的停炉时间可以适当减少。新炉第一炉的冶炼时间大于210分钟;修补炉第一炉的冶炼时间大于150分钟。 装第一批料,以8~10级电压供电,熔清后加入第二批料,以10~13级电压供电,基本熔清后启动康斯迪加料以15~17级电压供电。 当电炉回到水平位置后,启动康斯迪加料,根据冶炼进度、炉内温度和泡沫渣情况,控制合适的加料速度及供电曲线,一般以15~17级电压供电。冶炼中造好泡沫渣,做到埋弧操作,控制供氧强度,避免大沸腾现象发生。注意:电炉在生产过程中尽量避免有载调压!调压时提升电极,至电流归零,再调电压。● 跳电:在冶炼过程中,遇到电流波动过大(如塌料等),会产生跳电现象,跳电炉高压开关只要在主控室按“复位”按钮解除即可继续合闸生产;如跳33KV或220KV,则必须通知电工处理。● 允许合闸指示灯不亮:检查“F7”供电条件是否满足。碳粉喷入量设定范围为20~50 kg/min,以确保炉内泡沫渣良好为宜。氧气流量设定:小流量――1500~2000Nm3/h;大流量――3500~4000Nm3/h, 在第一、第二、第三批料熔化过程中不进行吹氧,第三批料熔化后,用碳氧枪小流量吹氧,同时视情况喷少量碳粉造泡沫渣。启动康斯迪后,增大碳粉量,氧气流量控制在小流量,碳粉喷吹流量控制在20Kg/min左右。 先启动水冷碳氧枪往炉内小流量吹氧喷碳形成泡沫渣后,再通电进行正常的冶炼操作。根据炉内钢水量确定氧气流量;装入量未达35吨之前用小流量供氧,35吨后用大流量供氧。确立先进枪后通电的原则,废钢未进到炉内不得使用大流量氧气供氧;熔池温度低时碳氧枪以造泡沫渣为主,泡沫渣造好后碳氧枪以切割废钢为主。 控制好炉内渣量,适量适时流渣,造好泡沫渣,埋弧升温。注意:根据配碳量、废钢情况和实时炉况合理控制氧气使用流量及枪位,防止钢水过氧化及大沸腾。3.1.1装入量接近和达到目标值 ,便进入升温阶段,当熔池温度达到1550℃左右时取第一个样作全分析,(如果炉内进有冷钢则要等冷钢基本熔化再取样);根据分析结果决定是否取第二个样。如果第一个样成分符合工艺要求,至熔池温度达到1580℃左右时取终点样;如第一个样〔C〕高,吹氧脱〔C〕后再取第二个样分析;如果〔P〕高,流渣后补加石灰和适量萤石造渣脱〔
P〕后再取第二个样分析,成分合格后至熔池温度达到1580℃左右时取终点样。在低合金钢的生产中为了有害元素的控制是一项基本的要求,一般包括:Cu、Ni、As、Sb、Sn、Pb、 Bi等,大多来源于废钢,为了控制微量有害元素的含量,尽量地降低损失,要求做到:● 在电炉熔清时发现微量有害元素超标则立即与储运调度联系,通知情况,并请储运调换废钢。● 对于已经送到康斯迪料场上的废钢必须与储运后送的废钢搭配方可入炉。● 对于电炉炉内已经发生的微量有害元素超标的情况,电炉出钢时必须尽量多倒出炉内钢水,请示领导处理。● 当班发生的微量有害元素超标的情况必须在值班记录上清楚反映,避免事故的重复发生。由于变压器输出功率和化学能相对稳定,溶池温度控制主要由康斯迪加料速度决定,为了保证溶池温度在碳沸腾温度范围,特殊能量控制在280~320Kwh/t为宜,此时炉内的钢水温度在1530~1580℃范围内。炉内钢水量达到目标值90~95%时,减慢康斯迪加料速度,提升溶池温度,并进行取样、测温操作。炉内钢水量达到目标装入量后,停止加料。● 合金加入量在1.2吨以上的钢种温度提高20℃,如果Cr铁、Mo铁加入量大,再提高20℃;● 冷炉、全新钢包、备用钢包等视情况温度各提高30±10℃。⑴、连接小车退出到“OUT”位,退出炉门碳氧枪;停电并将电极操作手柄打到“出钢”位置,摇炉控制权转移到炉后出钢操作台。以下在炉后出钢操作台上进行:⑵、电炉倾动到+2~5℃,打开EBT,如填料不能自动流出,可用氧气引流。⑶、当包内钢水5~10t时,随钢流将配好的精练渣、铁合金加入钢包内。铁合金的加入量以达到各钢种的合金成分下限为准,具体加入量可参考各钢种的《工艺操作要点》;精练渣加入量为10Kg/t钢。⑷、出钢量依据钢包车上的称量系统控制目标70-80t钢水,如称重系统故障,可依据倾炉角度从5°、9°、15°控制,各位置均有设定的出钢量,同时根据钢包内钢水液面以及钢包的包龄估计钢包中的钢水量。⑸、出钢量达到目标值时(目标值要随着钢包的状况随时调整),快速摇回电炉至-7°,同时启动钢包车退出,以防止氧化渣倒入钢包。
⑴、在冶炼Q215、Q235等普碳钢时在出钢时只加入0.5kg/吨钢铝饼进行预脱氧;⑵、在冶炼优钢、特钢时在电炉出钢时加入0.5~1.0kg/吨钢铝饼进行预脱氧;5.1 冶炼前期与正常操作一样,减少生铁加入量,炉内装入量控制在70t左右。为便于检查康斯迪设备,康斯迪料槽内的废钢料要走清。5.2 熔清后尽量流掉炉渣,使炉内渣量降到最低程度。5.5 炉中剩余的钢渣倒在备用钢包里,倒去上层氧化渣,剩余钢水倒入精炼炉钢包中。5.6 出钢完毕,检查出钢口,将水口下的残渣清理干净。关闭EBT,填好出钢口,摇平电炉,开始进入下一炉冶炼。● 炉前处理炉门专用叉车指定专人驾驶;配电操作由主操或付操作工操作。